Workplace Inspections, Audits & Assessments
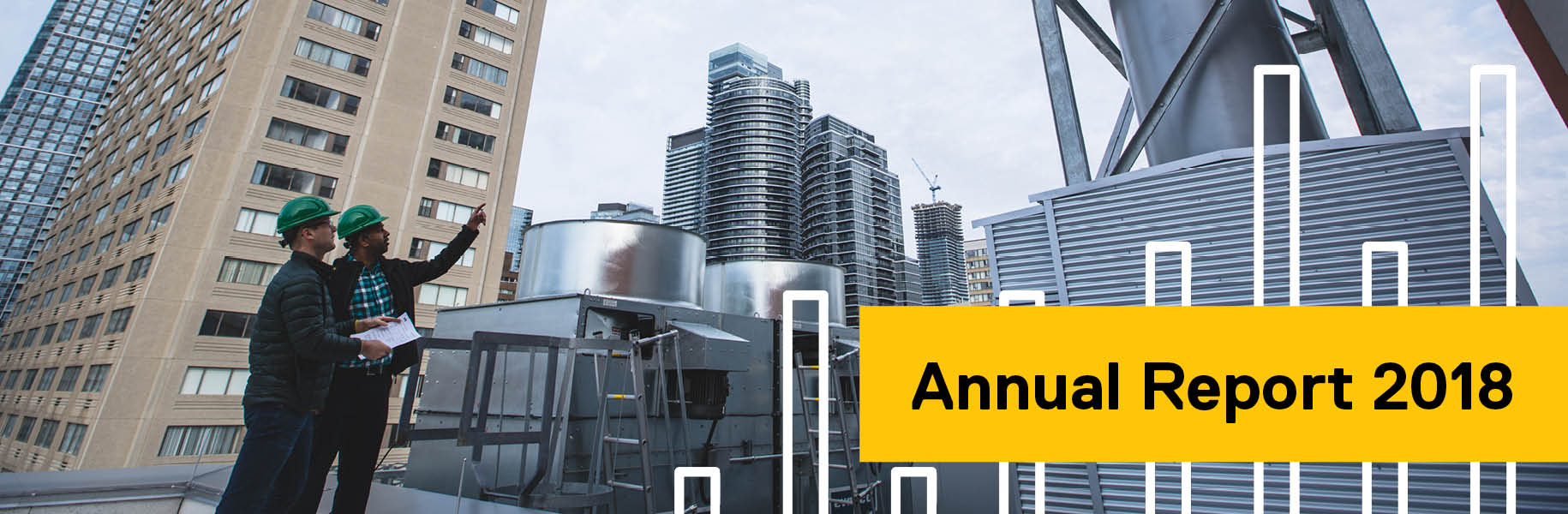
Safety workplace inspections are intended to proactively identify both existing and potential hazards that could result in injuries, illnesses and incidents to members of the TMU community.
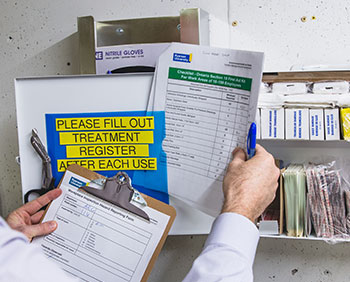
In 2018, EHS inspected 95% of 1200 medium and high risk spaces.

Physical workplace inspections
We monitor the inspection results closely and implement controls to manage the risks identified through:
- safe work procedures,
- policies,
- engineering controls,
- personal protective equipment, or
- addressing any repairs or maintenance measures.
In 2018, EHS and the Departmental Safety Officers focused on inspecting every workspace that included high and medium level risks, such as spaces that include machine shops, laboratories, and mechanical rooms. Due to the work and research being conducted, these spaces can have machine guarding, biological, ergonomic, chemical and physical hazards.
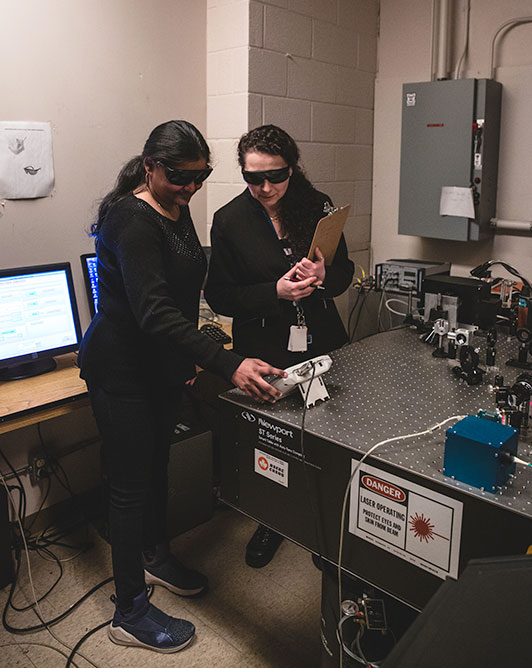
Inspections of medium and high risk workspaces in 2018
Over 940 spaces were inspected in 2018. These represent 95% of our medium and high risk spaces. Congratulations to Student Affairs, Provost and Vice President Academic, FOS, FEAS, FCS, FCAD and FOA for completing 100% of their inspections. Well done!
Specific laboratories and emergency equipment safety inspections
TMU has many specific laboratories (e.g., radiological, biological and laser laboratories) and many pieces of equipment in the labs that we inspect and certify annually including:
- fume hoods,
- emergency eyewash and safety showers,
- biosafety cabinets, and
- laminar flow hoods.
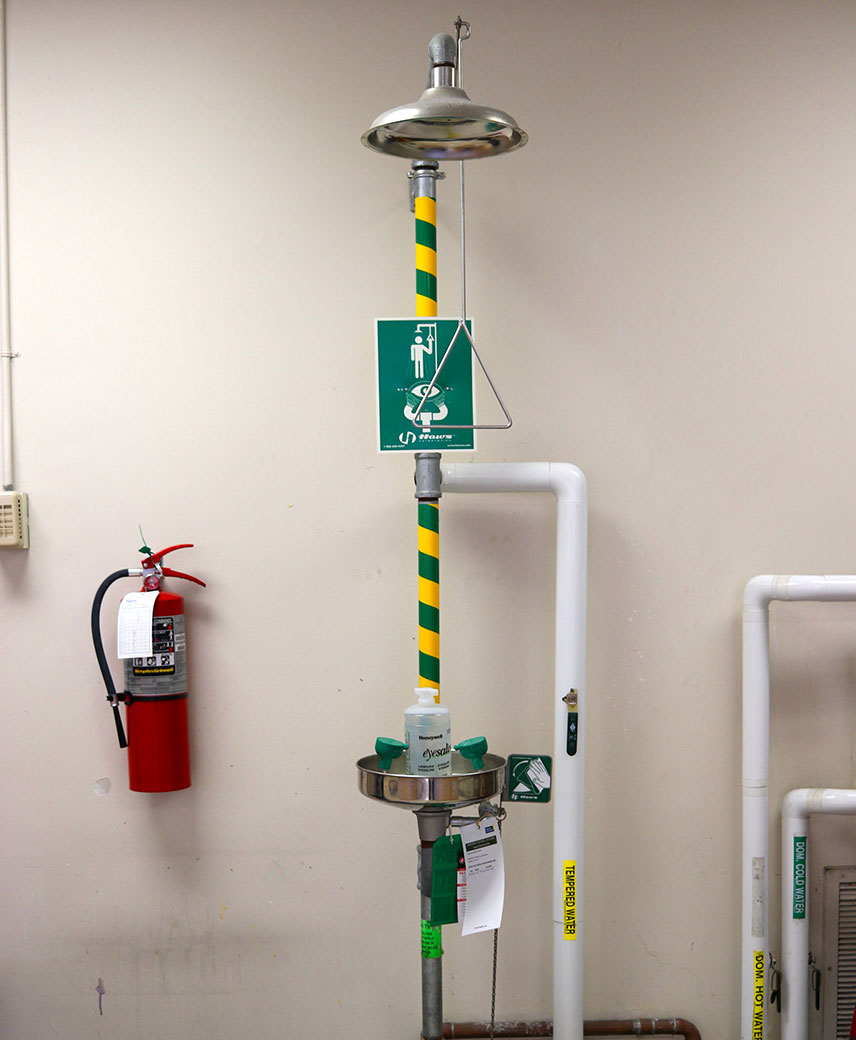
This table shows the number of completed safety inspections for in safety equipment. The equipment includes x-ray equipment, lasers, fume hoods, biosafety cabinets, laminar flow hoods, local exhaust arms, and emergency eyewashes and safety showers.

Racking assessment
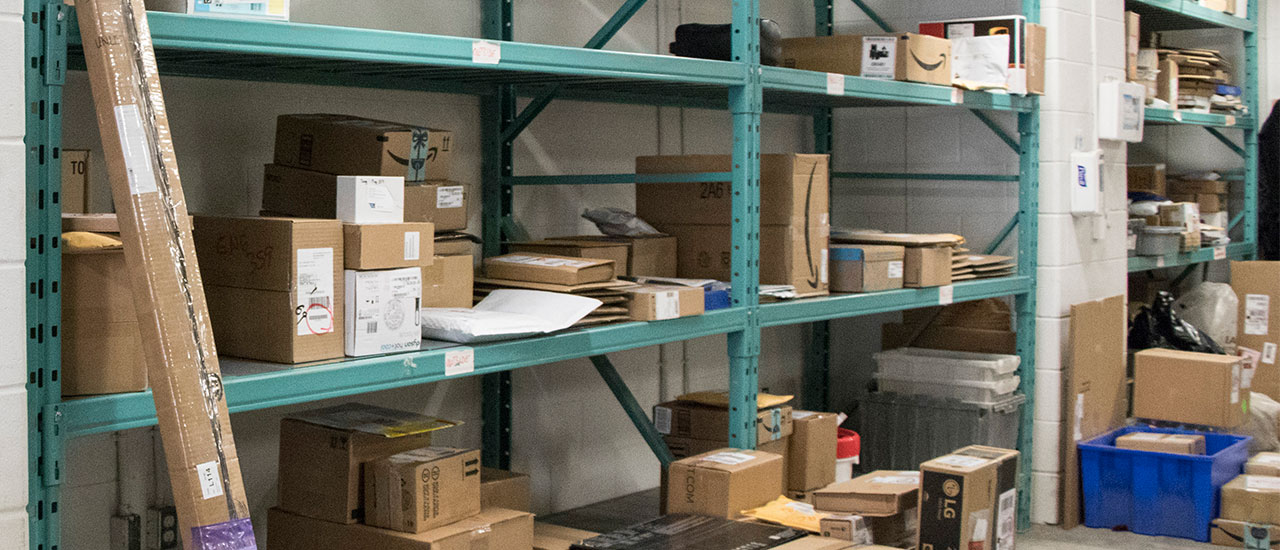
Racking is used across the university for storage. It poses a high injury risk if shelving collapsed due to poor installation and maintenance. To prevent this, racking needs to be anchored to the wall, structurally safe and clearly identify the load rating capacity.
In 2018, the EHS team coordinated a safety review of the 52 racking systems used across campus. Some key spaces reviewed include:
- the Sears engineering storage warehouse and workshops
- Interior Design
- Shipping and Receiving spaces
Key results from the safety review included:
- specific racking issues, such as improper loading on shelves, main beam deflection etc.
- general issues, such as not anchoring to the floor, secondary beam missing, pallets or materials resting against the racking system etc.
An action plan has been developed so that repair on structural deficiencies will be conducted by a dedicated rack service and repair specialist and recertified by an engineer.
In 2018, the EHS team coordinated a safety review of the 52 racking systems used across campus.
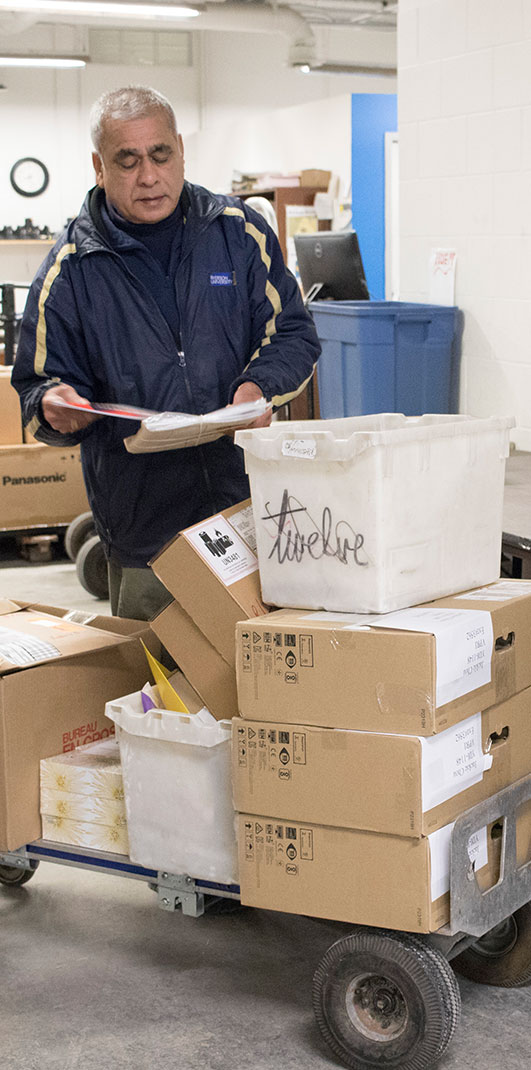

Machine guarding and emergency stops assessment
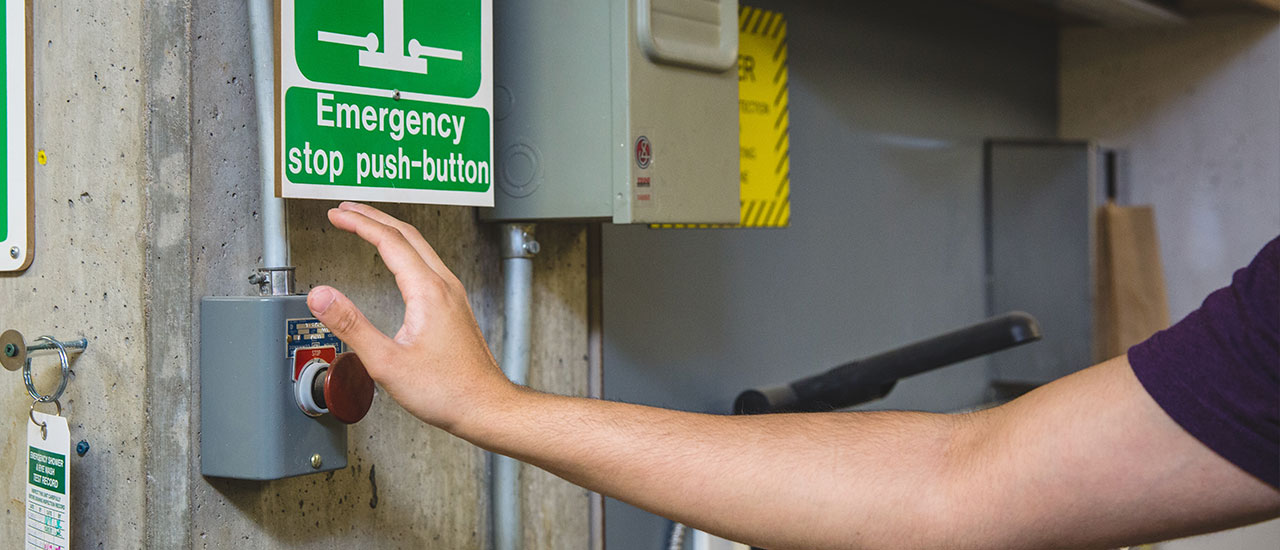
If the moving parts of machines are not properly guarded or locked out during maintenance and other activities, it can result in serious injuries such as amputation of fingers, limbs or death.
In 2018, TMU conducted a machine safeguarding and emergency stop review for machines in student-centric workshops. 143 machines at 15 locations with focus on machine guarding and emergency stops were assessed in:
- Faculty of Communication and Design
- Faculty of Engineering and Architectural Science
- Faculty of Science
- Facilities Management and Development department
The types of machines reviewed ranged from small lathes, saws, jointer, router, cutter, belt/disc sander to large CNC milling machine and robot.
In 2019, TMU will be addressing the gaps identified. This will complete our robust machine safety program that includes an e-learning module on machine safety and comprehensive Safe Operating Procedures for all our student-centric machines.
In 2018, TMU conducted a machine safeguarding and emergency stop reviews for 143 machines.
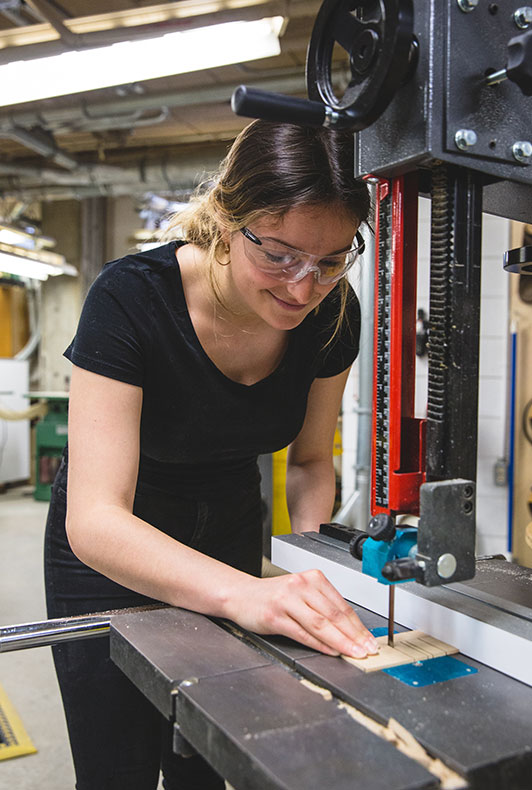

Noise and hearing conservation
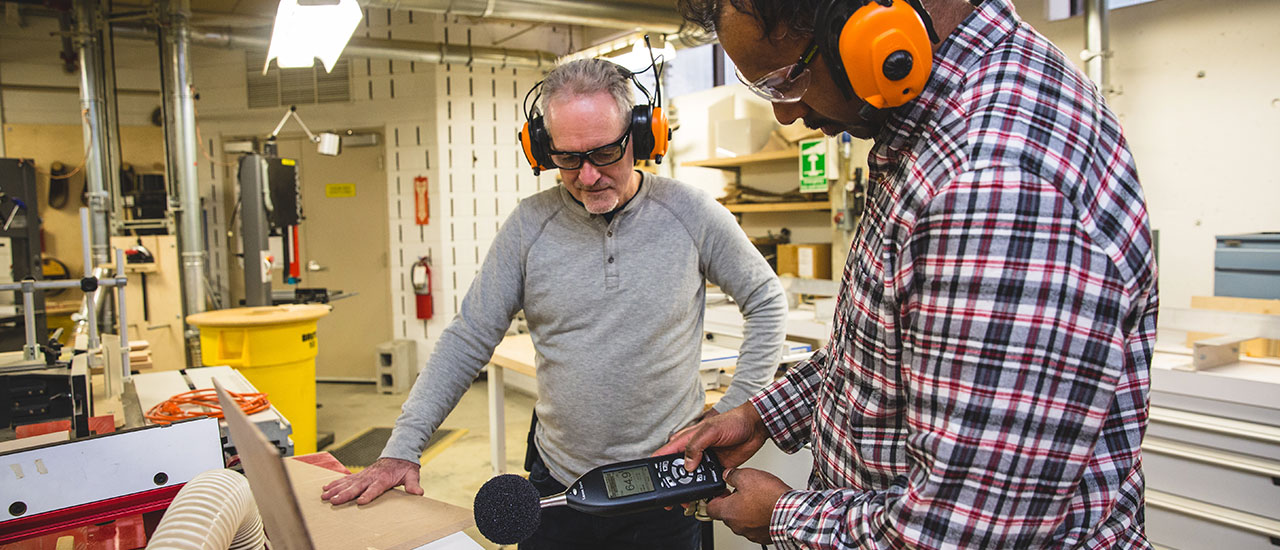
Excessive noise exposure can pose a serious health hazard over time, include noise induced hearing loss (NIHL), physical and psychological stress, a reduction in productivity. It can also interfere with communication. All of these impacts significantly contribute to workplace incidents and injuries.
Faculties and departments who participated in the assessments included Facilities Management and Development, Faculty of Science, Faculty of Communication and Design, Faculty of Engineering and Architectural Science and Ted Rogers School of Management.
Signage and the provision of hearing protection controls are being implemented in these areas.
Noise assessments training and control program
- Faculty of Science
- Faculty of Communication and Design
- Faculty of Engineering and Architectural Science
- Ted Rogers School of Management
- Mechanical rooms
103
noise assessments were completed where noise sources are known or assumed to be high. The regulatory limit of noise exposure over an 8 hour work day in Ontario is 85 dBA.
4
training sessions were completed for areas where noise levels were at or above the regulatory limit.


Designated substances assessment
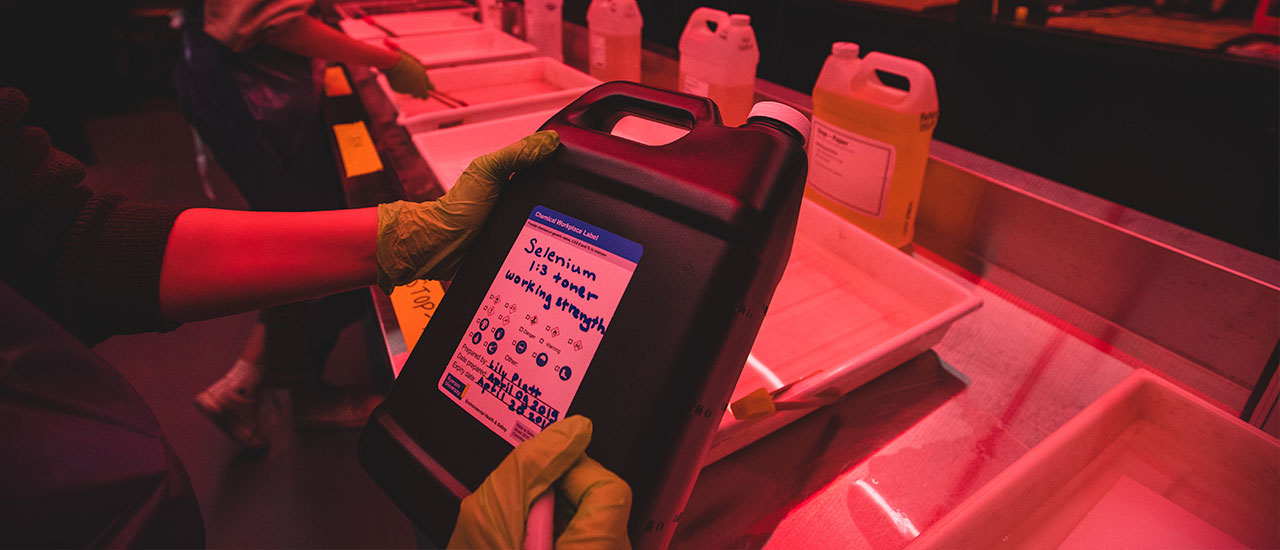
The Ontario Regulation 490/09 on designated substances includes 11 substances (external link) . When these are present, employers must conduct an assessment to determine the likelihood of worker exposure. When there is a possibility of worker exposure, a control program must be instituted that includes engineering controls, work practices, hygiene practices, record keeping and medical surveillance, if applicable.
In 2018, TMU completed a university-wide inventory of all our designated substances in areas of the university where designated substances were known to be handled. Main locations included:
- Mechanical and Industrial Engineering
- Chemical Engineering
- Civil Engineering
- Aerospace Engineering
- Chemistry and Biology
- Architecture
- Image Arts
- Physics
- School of Interior Design
- School of Performance
- Facilities Management and Development
The objective of the assessment was to determine the likelihood of worker exposure during normal use and in emergency situations.
In 2018, TMU completed a university-wide inventory of all our designated substances in areas of the university where designated substances were known to be handled.
Coming up in 2019
In 2019, EHS will work towards the development of a formal program for designated substances to improve on existing controls where necessary to mitigate any potential exposure risks to these substances.
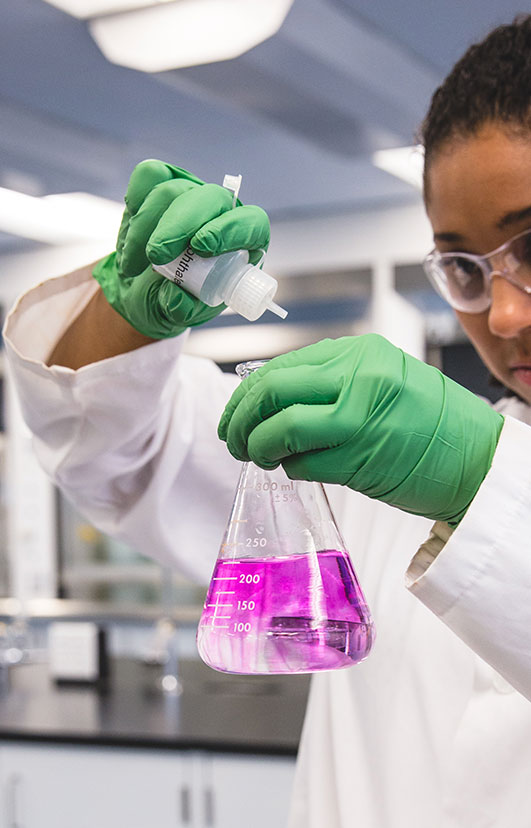

Federal Canadian Nuclear Safety Commission Audit
The Canadian Nuclear Safety Commission (CNSC) is the federal regulator of nuclear power and radioactive materials in Canada.
In 2018, the CNSC conducted an audit of TMU’s Radiation Safety Program to verify the conditions set out by the university’s Nuclear Substance and Radiation Devices licence. The audit included an inspection of all locations on campus where nuclear substances are used and stored.
The university successfully passed the audit with no non-compliances found or orders issued.

In 2018, TMU’s Radiation Safety Program successfully passed the CNSC audit.