Workplace Inspections, Audits & Assessments
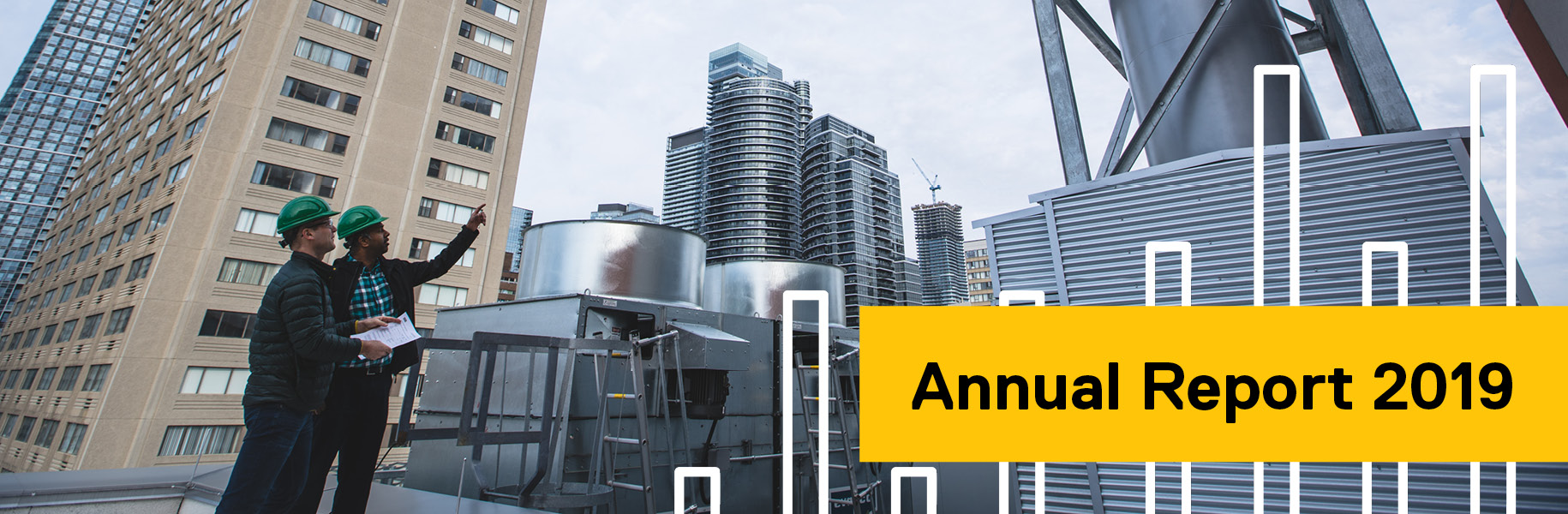
The university has a duty to ensure that work areas have been inspected on a regular basis so that risks are identified and adequately controlled. This means that part of a workplace is inspected monthly, so that the whole workplace is inspected at least once a year.
Health and safety workplace inspections are intended to proactively identify both existing and potential hazards that could result in injuries, illnesses and incidents to members of the Ryerson community.
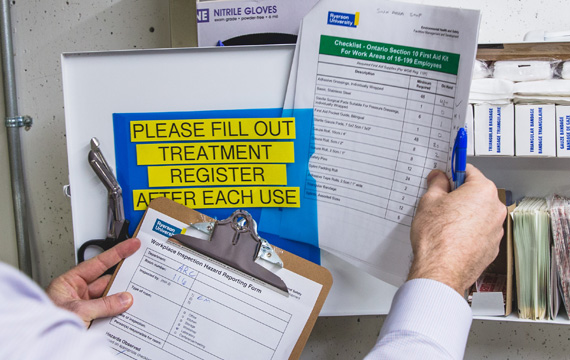
In 2019, 93% of all Ryerson spaces were assessed. This is approximately 5,100 work areas making up over 3 million square feet of space! It includes academic spaces such as laboratories, workshops, classrooms, non-academic spaces, as well as shared common facilities.
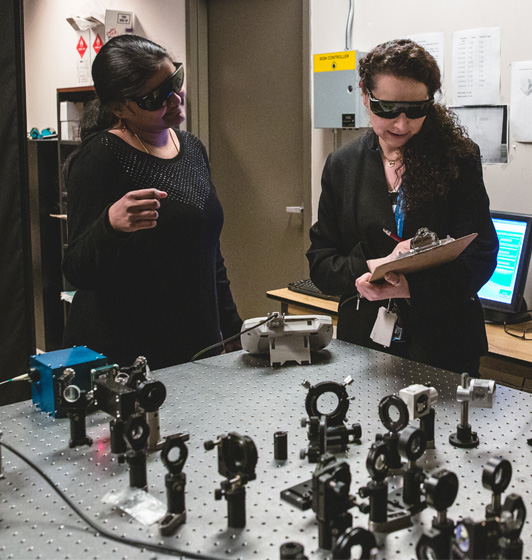
Due to the continued growth of our campus, Ryerson’s Joint Health and Safety Committee, along with EHS, streamlined this process by designating two full-time EHS employees to oversee the workplace inspection process. In partnership with the Facilities Management and Development maintenance and operations team, over 275 work orders were generated and closed out.
In addition to the revised workplace inspection process, Ryerson has procured a new web-based software system, Intelex. This was an initiative to help improve the efficiency of the process by removing administrative steps such as manual entries of workplace inspection and actions. These inspections can now be completed on hand-held devices to reduce paper waste and improve reporting efficiencies. Departments have designated, key system users to close out actions in their respective areas.

Specific laboratories and emergency equipment safety inspections
Ryerson has many specific laboratories (e.g., radiological, biological and laser laboratories) and many pieces of equipment in the labs are inspected and certified annually including:
- fume hoods,
- emergency eyewash and safety showers,
- biosafety cabinets, and
- laminar flow hoods.
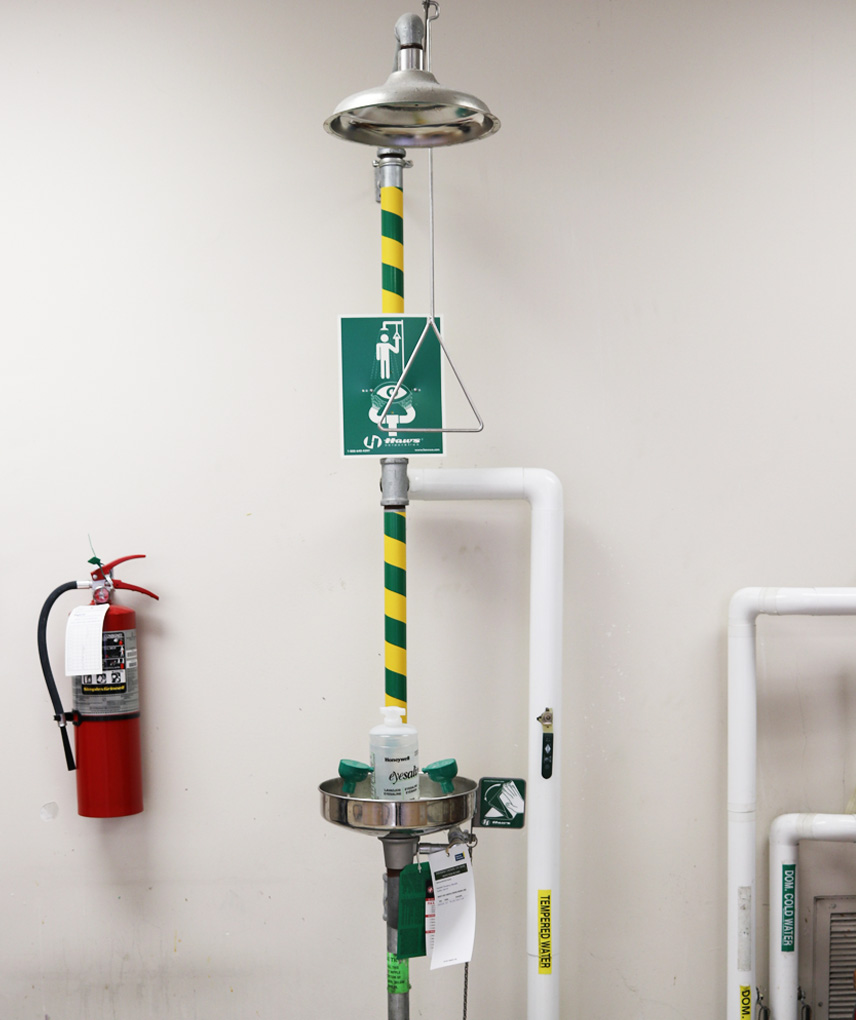
358 safety inspections
were completed in 2019.
This table shows the number of completed safety inspections for safety equipment.
In some cases, there were less frequent lab inspections in 2019 compared to 2018 as some labs were inactive due to renovation or waiting for relocation and therefore did not require inspection.
Additionally, four new laser systems were inspected in 2019.

Machine Safety Upgrades
In 2018, EHS started a project to address machine safety (including machine guarding and emergency stop) deficiencies across the university. This project includes over one hundred machines in high-risk workshop areas.
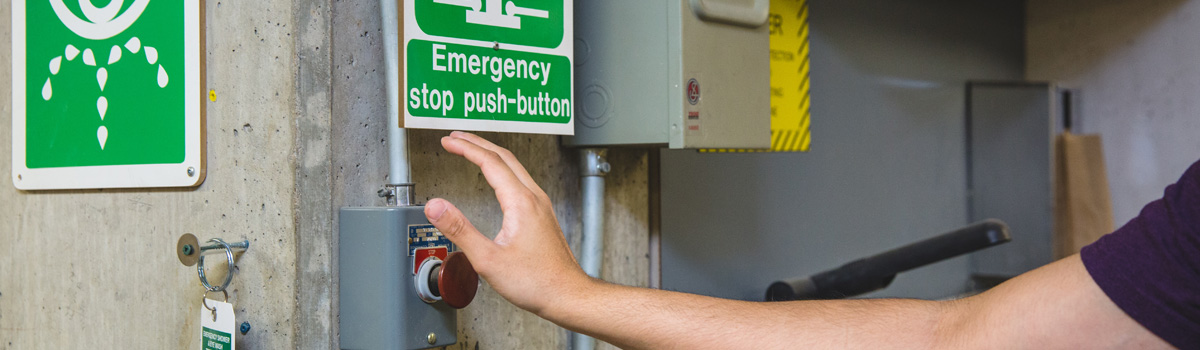
Milestones for this project include:
A third-party assessment of machine guarding and emergency stop deficiencies. This was completed in 2018.
In consultation with each affected faculty and administrative department, prioritization of repairs and developing a scope of work to address the deficiencies identified in the 2018 assessment. This work was completed in 2019.
The corrective work for all machines has now been successfully tendered and is expected to be completed by the end of 2020.